November 30, 2024
Polyfluoroalkyl substances (PFAS) are man-made chemicals developed in the 1940s that have been used in consumer products and manufacturing processes worldwide ever since. Incredibly resistant, PFAS have been used to make water-repellent clothing, stain resistant fabrics, nonstick cookware and cosmetics, but also in the production of mRNA vaccines and semiconductors. Their very resistance however means they do not break down naturally and remain in the environment forever and, most concerning, can accumulate in living organisms leading to harmful health effects in humans such as increased risk of cancer, high cholesterol levels and changes in liver enzymes. In this interview Henrik Hagemann tells us how Puraffinity is tackling the PFAS crisis.
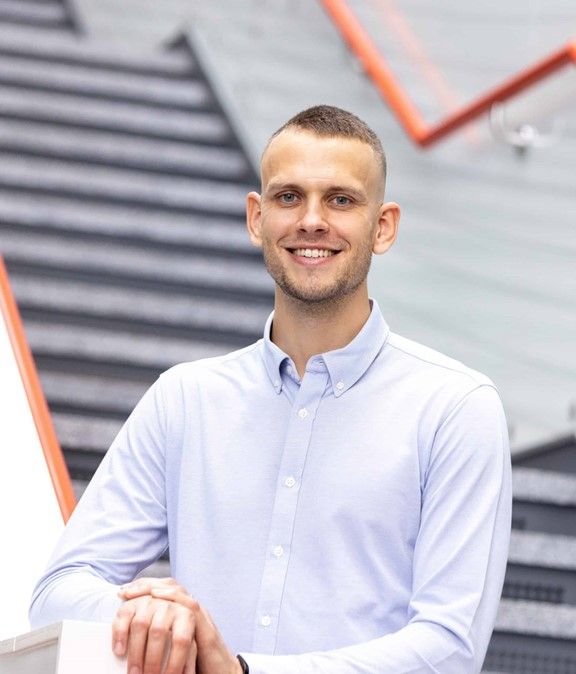
Henrik Hagemann
CEO and Co-Founder, Puraffinity
Henrik Hagemann is CEO and Co-Founder of Puraffinity. A Verve Ventures portfolio companysince 2019, Puraffinity develops engineered biomaterials that target Polyfluoroalkyl substances (PFAS) in contaminated water. In 2019, Henrik was on Forbes’ 30 Under 30 Europe list and MIT Tech Review’s 35 Under 35 Europe list. He has been part of the Diversity and Inclusion Steering group at the Royal Academy of Engineering for the last five years and together with co-founder Gabriella Santosa, strives to build Puraffinity into a startup with equity, diversity and inclusion at its heart. Henrik has a master’s in biomedical engineering from Imperial College London where he was an honoree of the President’s Medal for Outstanding Achievement.
First of all, what makes PFAS so terrible?
We’ve come to rely on PFAS as a society. They allow us to make everything from spacesuits to mRNA vaccines to semiconductors and enable the net zero electrical vehicle journey. They’re very useful. The downside is that what makes them useful also makes them very toxic. PFAS have three properties that make them terrible. One is that they have a very stable chemical bond so they stick around for much longer in the natural environment and the human body. That’s why people call them Forever Chemicals.
Another worrying property is that they accumulate in the body, so they build up over time as you get exposed to them through the air or water. And the third one, which is what struck me when I first learned about this back in 2016, is that they are a lot more toxic than arsenic. I knew about arsenic being poisonous from things like theater plays where a character pours it in somebody’s drink and they die the next day. Turns out that these PFAS chemicals are fifty times more toxic than arsenic.
“Unsafe levels of PFAS have been found in most rainwater on the planet, including in Antarctica.”
To add fuel to the fire, according to recently published research from Stockholm University and ETH Zurich, environmental contamination with PFAS has now exceeded the planetary boundary: unsafe levels of PFAS have been found in most rainwater on the planet, including in Antarctica. That’s the dilemma we’re facing.
How did you decide to start a company to address this issue?
When I was a bioengineer at Imperial College, we took part in a large synthetic biology competition in 2008. We presented a project that used sustainable approaches to precision materials to target the most toxic substances in water such as metals, oxyanions, pharmaceuticals, pesticides, and dyes.
When we presented the research project, it was just an idea. But when we came back to London, and we had won some awards, we were encouraged to look at how this approach to water filtration could be turned into a company. That led us to do a lot of customer discovery. And all the time when we were talking to these prospective customers, they were saying, filtering out metals is good, but what about perfluorinated compounds – this is what they called PFAS back then – can you take care of that? In the beginning, I just ignored it. But then, sports equipment manufacturers talked about using PFAS for making waterproof shoes, airport executives mentioned PFAS in firefighting foam and oil and gas companies talked about fireproofing oil extraction sites with hydraulic fluids that sometimes contain PFAS. It was frustrating, why were they all pointing to the same thing? So probably out of frustration, we started focusing on PFAS back in 2016. And then PFAS became an official term in 2017. And we’ve stuck to it.
How much public awareness is there concerning the dangers of PFAS?
The PFAS issue is known. But it took a big Hollywood movie like Dark Waters talking about a PFAS-related legal case for people to really become aware and concerned about the issue. They started asking themselves why their government isn’t taking care of this problem.
The highest level of awareness however is limited to communities that have been impacted directly, like Fayetteville, North Carolina, or West Virginia in the US where they had a plant that used PFAS. People got black teeth, high blood pressure or even died from cancer because of the level of contamination. In Europe, there are a few countries that had a PFAS-related crisis. In Denmark, there is this factory quite close to where I grew up, and the cows in the area were drinking water that had been contaminated with PFAS because of the use of firefighting foam. At one point, people realized they were eating meat that had PFAS in it. As a result of such incidents, awareness levels are increasing.
How does Puraffinity address PFAS?
Just to be very clear, when it comes to PFAS, we need a cradle to grave solution. It’s not enough to capture PFAS, you need to think of the full disposal route. At Puraffinity, it took us six years to design, build and test a tangible product that has been precision engineered to capture PFAS. It’s a bit like a small Lego brick that clicks onto PFAS only when it flows through a water column. It can capture PFAS 10 times faster than existing methods. But that’s not enough. One of the many issues we ran into in this field was that you have to optimize across multiple parameters, not just performance, but also stability, safety, longevity, and cost effectiveness.
We went from having an early prototype in 2017, that had superior performance in the lab stage to spending the last four years developing a material that has a longer lifespan. We’ve done some studies that will be coming out soon with third party validation looking at three times longer lifespan, as well as the reaction rate, stability and safety of the material.
Our solution captures PFAS with a reusable approach. So instead of throwing away the material every time it’s been filled up with PFAS, you can unclick the bound Lego bricks with a step called regeneration. And then you can reuse it which makes it both cost-effective and sustainable because you’re no longer throwing away the material every time you use it.
What happens to the PFAS after regeneration?
Right now we’re working on integrating emerging destruction technologies into the cycle. The Dichtel research group at Northwestern University recently had a breakthrough with developing a new PFAS destruction method. Supercritical water oxidation, a green technology used to treat hazardous wastewaters, can also be used to destroy PFAS. We are working to have a destruction method whereby the regenerated PFAS goes into a small concentrated solution called eluate. This much smaller volume of eluate waste then gets destroyed through sustainable destruction methods, eliminating PFAS.
Since PFAS continue to be used, can’t they be reused after regeneration? So rather than having it be a cradle to grave solution, can its use not be cyclical?
That’s the second phase of our roll out. We have been part of an Ellen MacArthur Foundation project looking at the reuse of PFAS. One of the main disadvantages of destruction is that you’re destroying something which has been designed to not be destroyed. You’re wasting a lot of energy, it’s very unsustainable. You could reuse PFAS for lower grade applications such as the automotive chrome plating industry, for example, where a perfect concentration of PFAS isn’t always needed. That’s one of the benefits of having a targeted adsorbent to capture PFAS. But I should be clear, PFAS reuse is not something that’s been scientifically de-risked yet.
What does the competition look like in this space? Is there anyone else doing what you’re doing?
There are two camps when it comes to addressing PFAS. One wants to put out the fire right now, because the PFAS crisis is a bit like a wildfire. This category uses existing materials such as ion exchange columns and activated carbon to filter PFAS. Ion exchange resins were developed 80 years ago and are used for treating water problems such as hard water and scale buildup. Companies have now repurposed them to capture PFAS, but removing PFAS reduces the lifespan of ion exchange columns from 6-12 months to two weeks. Similarly, with activated carbon, it’s not been designed to remove PFAS. You therefore need to use a lot of material to filter out PFAS and then what do you do with it? Often, it goes to landfills, or it’s sent to be destroyed at an incineration plant where it’s not always fully destroyed.
The other camp is developing new technologies that are very promising. These are things like targeted absorbents which are being developed by companies like Cyclopure and CETCO. Unfortunately, some of them use PFAS chemistries in the material itself and that’s like fighting fire with fire. We don’t want to be introducing new PFAS products to capture PFAS. That, to me, has a clear disadvantage. However, most of the competition is focusing on developing new destruction methods right now which are all very complementary to us.
The UN Chemical Regulators banned most PFAS under the Stockholm Convention in 2019. What does that mean for Puraffinity?
They have started to ban PFAS across a lot of applications, which is what we need. We have to reduce it first, then prevent it and focus on targeted capture. I always say to my team, even if PFAS was completely banned now, there is 200 years of treatment required for the existing sites that have been contaminated. That’s how much we’ve been using PFAS. Secondly, is it realistic that we will stop making mRNA vaccines? Can we stop making semiconductor chips? Can we find a chemistry which is as stable as PFAS? It’s really challenging.
Is mitigation of PFAS risks likelier than the development of less toxic chemical alternatives?
I think we need to do both, the main problem here is time. We cannot afford to wait. We need to take the risk of trying to build new technologies to get alternatives to PFAS. For existing applications using PFAS, we need to take a circular approach. We need to have PFAS contained within the factories. That’s what they’ve been doing with other chemistries, like refrigerator fluids, which are also dangerous compounds. If you can reuse them and keep them in these factories, then we have a much better approach.
This kind of circular approach makes sense when PFAS are used as part of the manufacturing process, but what about products such as waterproof cosmetics, raincoats and so on that have PFAS as a component?
For many of these things, we need to eliminate it from the product. We cannot have dental floss that contains PFAS, we cannot have a cosmetic product that contains PFAS. That’s where we need to focus on alternative chemistries. And maybe we do need to compromise a bit on performance, like my raincoat won’t be as good, but at least I won’t die from being exposed to PFAS. I think we need to focus on these applications where PFAS is part of the product first. But there are many applications where PFAS is just part of the manufacturing process. For an mRNA vaccine, it’s not in the final product, it’s just used in the tubing to make the product. For semiconductor chips, it’s used to enable the deposition of materials at the nanometer scale. These are sites where you can use PFAS sustainably if you have a closed loop system.
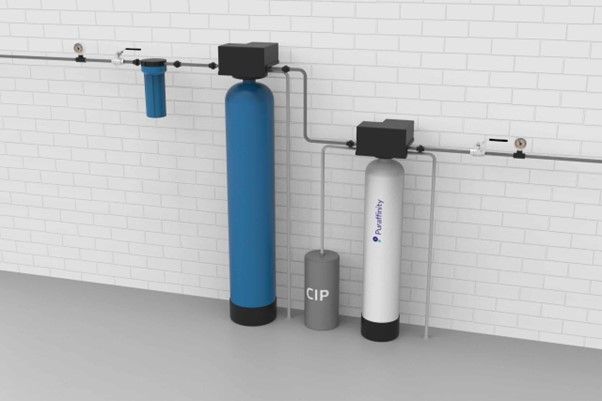
Full household Purrafinity system, able to handle PFAS treatment for 100k gallons of water.
What is your go to market strategy?
We want to first certify the product to something like the US National Sanitation Foundation (NSF) standard for its stability and its safety, so that we can certify that you’re not introducing anything bad to the environment by using this material. The NSF certification is focused on the US but is also seen as a positive in Europe. The market for us is very US-centric, but it also has a strong European angle. We have been doing tests with possible clients in Germany, Sweden, France, and the UK. We see an increasing awareness of the need for products such as ours in Europe in response to changes in the 2020 EU Water Framework Directive. These changes were primarily a response to the pandemic when PFAS was connected to a possible disruption in the efficacy of vaccines. The new 2021 EU regulations include 10 times more PFAS species than they used to.
In the US, there was a huge shift this year, with regulations becoming 1000 times stricter than in 2016. The Environmental Protection Agency has now reduced the advisory PFAS concentrations more than 35 million fold since 2009 alone. There are about 57,000 sites that are PFAS contaminated in the US. Many people living on these sites are trying to access funds for remediation. If they are successful, that would be another big change as then there would be a budget for it from the Federal government which would be useful.
How is the scale up process going for Puraffinity?
We’ve scaled up manufacturing here in the UK with outsource manufacturing partners to about 5 tonnes production capacity which would roughly translate to about 250,000 devices for a point of use application. That’s when you fit cartridges in communities impacted by PFAS, so they can remove PFAS from their tap water. For the next step, we’ve brought in David Bent who is a former Dow Corning production director, who has scaled up processes across the last 30 years. We’re aiming to get to 150 tonnes production capacity next year which we’ll do through outsourced manufacturing as well.
One of the beautiful things about doing sustainable green chemistry processes is that often, you can rent time on existing outsourced manufacturing plants. So we haven’t had to build our own production plant yet. And that’s been very deliberate. We have this initial wave of doing outsource manufacturing to demonstrate the commercial traction and get to millions of pounds in revenue. Then, based on that, we want to create our own factory in 2025 and integrate all the learnings and IP from this first wave into it. We will continue with this network of diversified outsource manufacturers even when we have our own plant so we’re not just relying on a single site.
Article source:
https://www.verve.vc/blog/pfas-chemicals-are-fifty-times-more-toxic-than-arsenic/
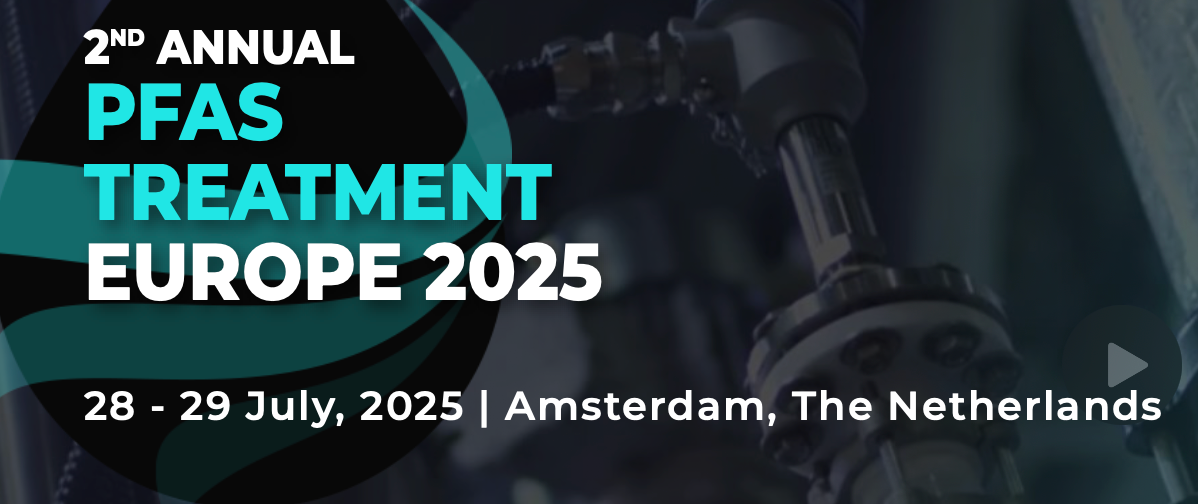
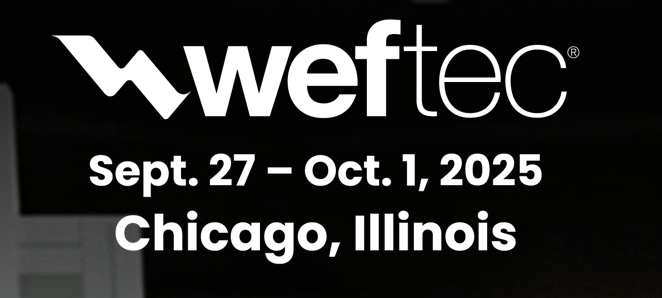
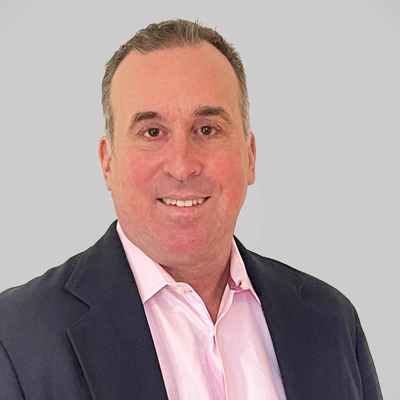